London Borough of Newham Tower Block Recladding Programme
London Borough of Newham required an immediate response to keep residents safe in the wake of the Hackitt review.
The brief was to remove the aluminium composite material cladding from four tower blocks and protect the health and safety of the residents there. The stakeholders were London Borough of Newnham asset management, housing management and health and safety teams. Given the sensitive nature of the project, other stakeholders included local councillors, the Mayor, strategic team, local residents’ groups, London Fire Brigade, building control, and the wider neighbourhood, as well as the residents themselves.
There was no industry guidance at the time in relation to fireproof materials and type of cladding materials together with the reconstruction of new cladding. The brief included the research of these criteria and work with the Building Research Establishment and
other bodies to recommend the best course of action. The brief was also to review and implement an emergency procurement process to appoint a contractor to avoid delay and to meet the value for money criteria. Following removal of sample cladding we identified the lack of fire barriers which led the client to appoint fire marshals 24 hours per day to protect the residents for fire evacuation.
Conflicting information on building safety, cladding materials and fire protection following the Hackitt review created substantial challenges for us. We had to learn and adapt fast to this complex information. We brought in additional RICS qualified
building surveyors specialising in fire safety to assist the project team and we created a knowledge centre network with other specialists as well as the Building Research Establishment. During the project, each design was reviewed in line with current compliance as well as good practice. Based on this we enhanced the design features to install extra fire barriers. The clerk of works visited site weekly, and the inspection report was closely checked. We decided to implement new processes for project review and quality inspection.
We implemented an effective communication system using our defects database for reporting and managing defects. A dedicated person was allocated to defects enquiries and these were immediately passed to the appropriately trained team. The defects sheet was also copied to our clerk of works who visited the site after rectification. We could not achieve zero defects, but the defects were negligible as the quality was very high. This was achieved by a small area snagged with all parties before allowing the contractors to progress to wider areas.
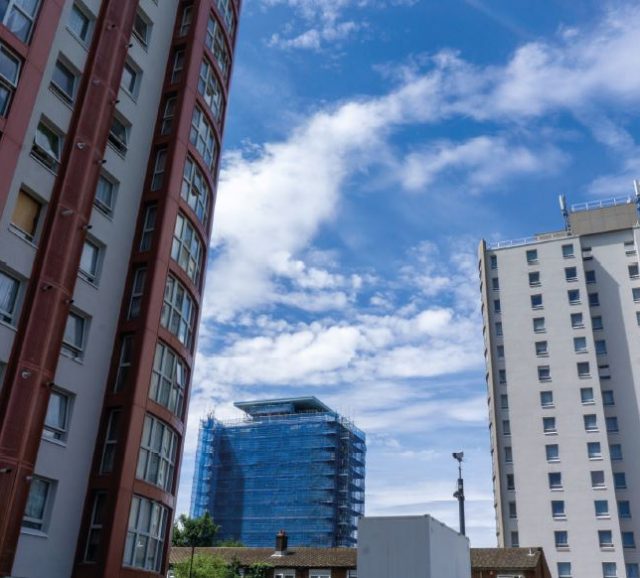
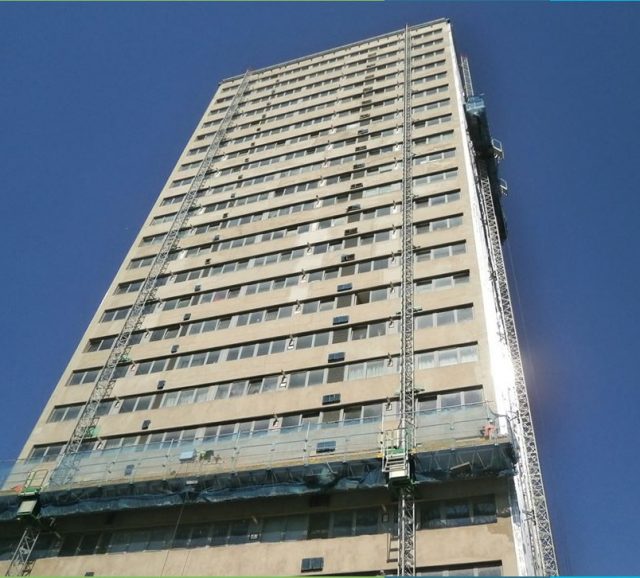

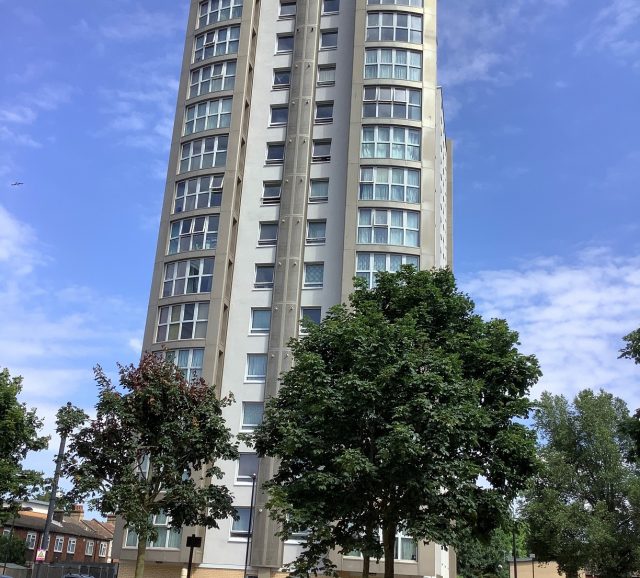
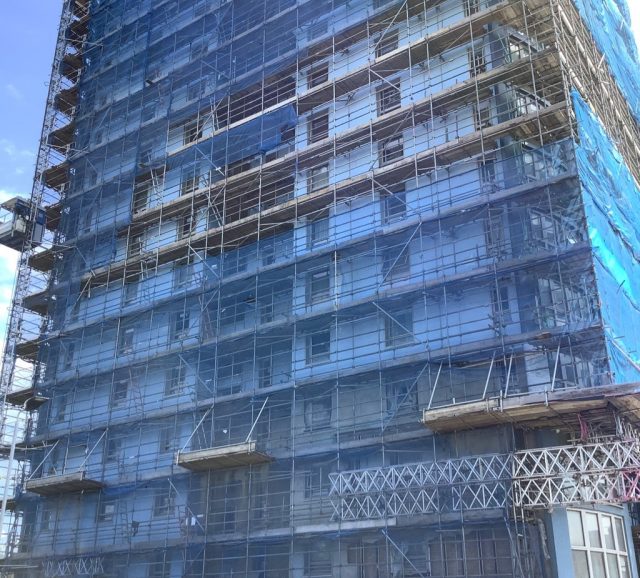
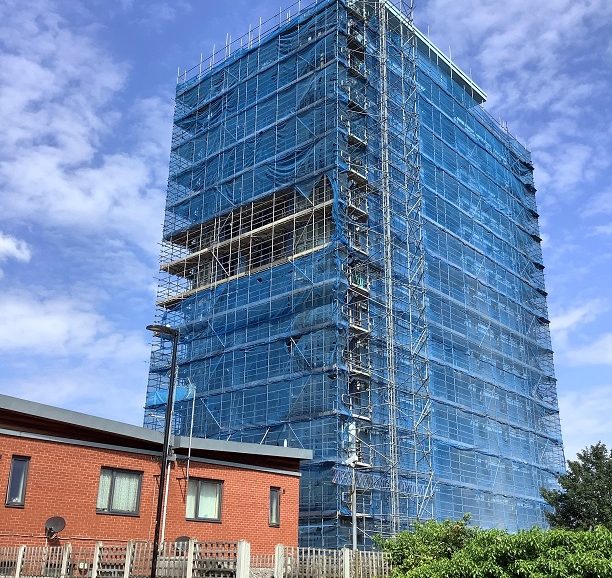
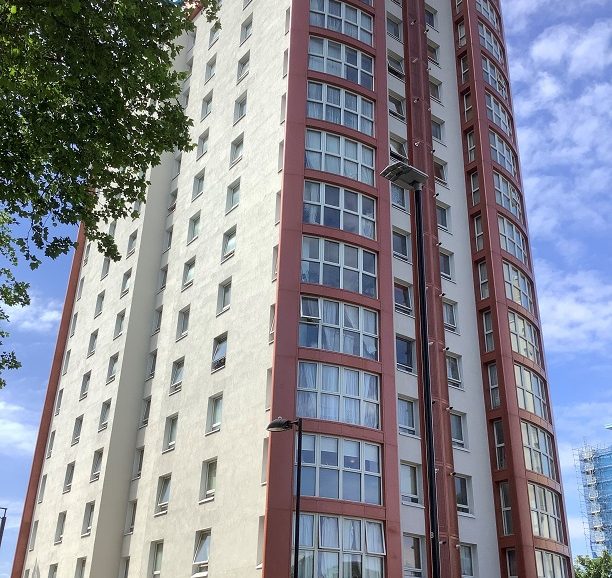